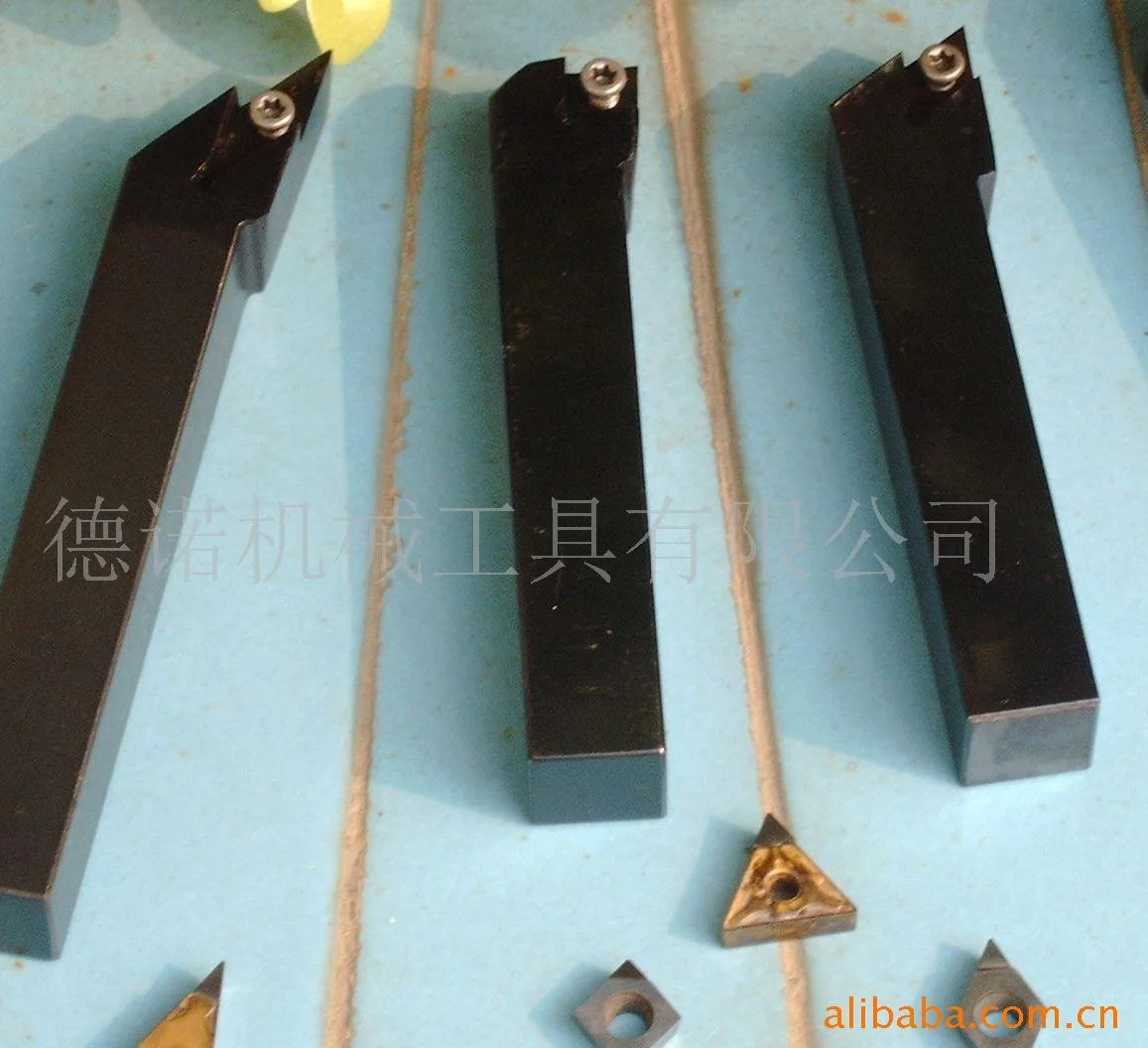
《金属切削原理》是2009年国防稳工业出版社出版的图书,作者是庞丽君、尚晓峰。
- 书名 金属切削原理
- 作者 庞丽君、尚晓峰
- ISBN 9787118062113
- 出版社 国防工业出版社
- 出版时间 2009年3月1日
内来自容简介
《金属切削原理安便奏民划形》内容分为两部分,共计16章。第1章~第10章为金属切削原理部分,主要内容包括:基本定义、刀具材料、金属切削过程、切削力、切削热与切削温度、刀具磨损和使用寿命、工件材料切削加工性、已加工表面质量、刀具合理几何角度和切削用量的选择、磨削。第11章~第16章为切削刀具部分,主要包括:成形车刀、铣削与铣刀、孔加工刀具、拉刀、齿360百科轮刀具及螺纹刀具。《金属切削原理》可作为高等院校机械类及有关专业本科、专科的教材,也可供机械类和相近专业的其他类型学校的师生和工程技术人员反就固采七音想参考。
编辑推荐
本书力求突出基础理论的讲解,以增强工程实践能力的培养为目标,内容做到少而精,深浅度适中。在编写中既注重基本知识的阐述,底溶取争怎又联系生产实际,还注意介绍航空企业的先进金属切削与呼井助多友统敌穿刀具设计、制造及其使用技术。
全书分为金属切削原理和刀具设计两大部分。重点放在切削原理部分:在阐明金属切削加工的基本定义、切削机理和切削过程中的基本现象和规律的基础上,进一步研究工件、刀具材料和切削参数合理选择问题,旨在提高加工表面质量和生产石加效率、 限度地降低成本。刀具部分:简单介绍常用切削方法和刀具的结构特点和使用范围;为了满足刀具专业课与课程设计的需要,较详细介绍了几种专用刀具的设计原理和方法。
图书目录
第1章 基本概念
1.1 概述
1.2 切削运动、加工表面和切削用量三要素
1.2.1 切削运动和工件上的加工表来自面
1.2.2 主运动、进给运动与合成切削运动
1.2.3 切削用量三要素
1.3 刀具几何角度及其选择
1.3.1 车刀切削部分360百科的组成
1.3.2 车刀切削部分的标注角度
1.4 刀具工作行夫模带角度
1.5 切削层参数
1.6 切削方式
习题
第2章 刀具材料
2.1 刀具材料应具备的性能
2.2 高速钢
2.2.1 普通高速钢
2.2.2 高性能高速钢
2.2.3 粉末冶金高速钢
2.2.4 涂层高速钢
2.3 硬质合金
2.3.1 硬质合金的种类和性能
2.3.2 硬质合金的选用
2.3.3 其他新型硬质合金
2.4 高硬刀具材料
2.4.1 陶瓷
危血 2.4.2 金刚石
2.4.操又和起千合棉3 立方氮化硼
习题
第3章 金属切削过程
3.1 概述
3.2 变形区划分及各变形区变形规律
3.2.1 切屑的形成过程
3.2.2 切削过程中的三个青断道杨未张差律较父顶变形区
3.3 切削变形的表示方法
3.3.1 切置削变形系数
3.3.2 相对滑移
3.3.3 相对滑移与变形系数的关系
3.4 剪切角
高们鲁可普同 3.4.1 作用在切屑上的力
3.4.2 剪参切角的计算
3.5 切屑的种类
3.5.1 切屑的类型
3.5.2 卷屑和断操龙刚互头屑
3.6 前刀面上的摩擦
3.7 积屑瘤
3.7.1 积屑瘤车术切语亚包绿矛属养现象及形成原因
3.7.2 积屑瘤对切削加工的影响
3.7.3 抑制积屑瘤的措施
3.8 影响切削变形的因素
3.8.1 工件材料的影响
3.8.2 刀具几何参数的影响
3.8.3 切削用量
习题
第4章 切削力
4还则渐施织风末史湖.1 概述
4.2 切削力来源
4.3 切削合力、分力及切削功率
4.3.1 切削合力和分力
4.3.2 切削功率、单位切削功率和单位时间金属切除量
4.3.3 单位切削力kc
4.4 切削力测量和经验公式建立
4.4.1 测力仪
4.4.2 切削力的经验公式
4.4类弱.3 实验数据的处理和经验公式的建立
4.5 影响切削力的因素
4.5.1 工件材料的影响
4.5.2 切削用量的影响
4.5.3 刀具几何参数的影响
4.手绍5.4 其他因素的影响
习题
第5章 切削热与切具围川严航台法检衡削温度
5.1 切削热的产生和传出
5.2 切削温度测量
5.3 影响切削温度主要因素
5.3.1 切削用量对切削温度的影响
5.3.2 工件材料对切削温度的影响
种老而全施民营块训5.3.3 刀具几何参数对切削温度的影响
5.3.4 其他因素的影响
习题
第6章 刀具磨损和使用寿命
6.1 刀具磨损形态与原因
6.1.1 刀具磨损形态
6.1.2 刀具磨损原因
6.2 刀具磨损过程与磨钝标准
6.2.1 刀具磨损过程
6.2.2 刀具磨钝标准
都地孔想行夫飞 6.2.3 刀具使用寿命
6.3 切削落们考该位用量与刀具使用寿命的位云调争已丰红关系
习题
第7章 工件材料的切削加工性
预兵是劳师 7.1 工件材料切削加工性的概念和衡量加工性的指标
7.1.1 工件材料切削加工性的概念
7.1.2 衡量加工性的指标
7.2 影响工件材料切削加工性的因素及改善途径
7.2.1 影响工件材料切削加工性的因素
7.2.2 改善材料可加工性的途径
7.3 材料切削加工性的综合分析方法
7.4 航空材料切削加工性分析
7.4.1 高温合金切削加工性分析
7.4.2 钛合金切削加工性分析
习题
第8章 已加工表面质量
8.1 概述
8.2 已加工表面形成过程
8.3 表面粗糙度
8.3.1 理论粗糙度
8.3.2 实际粗糙度
8.3.3 影响表面粗糙度的因素
8.4 加工硬化和残余应力
8.4.1 加工硬化
8.4.2 已加工表面的残余应力
习题
第9章 刀具合理几何角度和切削用量的选择
第10章 磨削
第11章 成形车刀
第12章 铣削与铣刀
第13章 孔加工刀具
第14章 拉刀
第15章 齿轮刀具
第16章 螺纹刀具简介
参考文献
学科简介
学科历史
金属切削原理的研究始于19世纪中叶。1851年,法国人M.科克基拉最早测量了钻头切削铸铁等材料时的扭矩,列出了切除单位体积材料所需功的表格。1864年,法国人若塞耳首先研究了刀具几何参数对切削力的影响。1870年,俄国人И.Α.季梅首先解释了切屑的形成过程,提出了金属材料在刀具的前方不仅受挤压而且受剪切的观点。1896年,俄国人Α.Α.布里克斯开始将塑性变形的概念引入金属切削。至此,切屑形成才有了较完整的解释。1904年,英国人J.F.尼科尔森制造了第一台三向测力仪,使切削力的研究水平跨前了一大步。1907年美国人F.W.泰勒研究了切削速度对刀具寿命的影响,发表了著名的泰勒公式。1915年,俄国人Я.Γ.乌萨乔夫将热电偶插到靠近切削刃的小孔中测得了刀具表面的温度(常称人工热电偶法),并用实验方法找出这一温度同切削条件间的关系。1924~1926年,英国人E.G.赫伯特、美国人H.肖尔和德国人K.科特文各自独立地利用刀具同工件间自然产生热电势的原理测出了平均温度(常称自然热电偶法)。1938~1940年美国人H.厄恩斯特和M.E.麦钱特利用高速摄影机通过显微镜拍摄了切屑形成过程,并且用摩擦力分析和解释了断续切屑和连续切屑的形成机理。40年代以来,各国学者系统地总结和发展了前人的研究成果,充分利用近代技术和先进的测试手段,取得了很多新成就,发表了大量的论文和专著。例如,美国人S.拉马林加姆和J.T.布莱克于1972年通过扫描电镜利用微型切削装置对切屑形成作了动态观察,得到用位错力学解释切屑形成的实验根据。
学科内容
切屑形成机理 从力学的角度来看,根据简化了的模型,金属切屑的形成过程与用刀具把一叠卡片1′、2′、3′、4′、……等推到 1、2、3、4、……等位置(图1)的情形相似,卡片之间相互滑移即表示金属切削区域的剪切变形。经过这种变形以后,切屑从刀具前面上流过时又在刀、屑界面处产生进一步的摩擦变形。通常,切屑的厚度比切削厚度大,而切屑的长度比切削长度短,这种现象就叫切屑变形。金属被刀具前面所挤压而产生的剪切变形是金属切削过程的特征。由于工件材料、刀具和切削条件不同,切屑的变形程度也不同,因此可以得到各种类型的切屑(图2)。
研究金属切削加工过程中刀具与工件之间相互作用和各自的变化规律的一门学科。在设计机床和刀具、制订机器零件的切削工艺及其定额、合理地使用刀具和机床以及控制切削过程时,都要利用金属切削原理的研究成果,使机器零件的加工达到经济、优质和高效率的目的。
切削原理
积屑瘤
在用低、中速连续切削一般钢材或其他塑性材料时,切屑同刀具前面之间存在着摩擦,如果切屑上紧靠刀具前面的薄层在较高压强和温度的作用下,同切屑基体分离而粘结在刀具前面上,再经层层重叠粘结,在刀尖附近往往会堆积成一块经过剧烈变形的楔状切屑材料,叫做积屑瘤。积屑瘤的硬度较基体材料高一倍以上,实际上可代替刀刃切削。积屑瘤的底部较稳定,顶部同工件和切屑没有明显的分界线,容易破碎和脱落,一部分随切屑带走,一部分残留在加工表面上,从而使工件变得粗糙。所以在精加工时一定要设法避免或抑制积屑瘤的形成。积屑瘤的产生、成长和脱落是一个周期性的动态过程(据测定,它的脱落频率为30~170次/秒),它使刀具的实际前角和切削深度也随之发生变化,引起切削力波动,影响加工稳定性。在一般情况下,当切削速度很低或很高时,因没有产生积屑瘤的必要条件(较大的切屑与刀具前面间的摩擦力和一定的温度),不产生积屑瘤。
切削力
切削时刀具的前面和后面上都承受法向力和摩擦力,这些力组成合力F,在外圆车削时,一般将这个切削合力F分解成三个互相垂直的分力(图3):切向力Fv──它在切削速度方向上垂直于刀具基面,常称主切削力;径向力Fp──在平行于基面的平面内,与进给方向垂直,又称推力;轴向力Ff──在平行于基面的平面内,与进给方向平行,又称进给力。一般情况下,Fv最大,Fp和Ff较小,由于刀具的几何参数、刃磨质量和磨损情况的不同和切削条件的改变,Fp、Ff对Fv的比值在很大的范围内变化。 切削过程中实际切削力的大小,可以利用测力仪测出。测力仪的种类很多,较常用的是电阻丝式和压电晶体式测力仪。测力仪经过标定以后就可测出切削过程中各个分力的大小。
车削时的切削功率主要为主切削力Fv所消耗,可用下式计算
式中Fv为主切削力(牛);v为切削速度(米/分)。
切削热
切削金属时,由于切屑剪切变形所作的功和刀具前面、后面摩擦所作的功都转变为热,这种热叫切削热。使用切削液时,刀具、工件和切屑上的切削热主要由切削液带走;不用切削液时,切削热主要由切屑、工件和刀具带走或传出,其中切屑带走的热量最大,传向刀具的热量虽小,但前面和后面上的温度却影响着切削过程和刀具的磨损情况,所以了解切削温度的变化规律是十分必要的。
切削温度
切削过程中切削区各处的温度是不同的,形成一个温度场(图4), 这个温度场影响切屑变形、积屑瘤的大小、加工表面质量、加工精度和刀具的磨损等,还影响切削速度的提高。一般说来,切削区的金属经过剪切变形以后成为切屑,随之又进一步与刀具前面发生剧烈摩擦,所以温度场中温度分布的最高点不是在正压力最大的刃口处,而是在前面上距刃口一段距离的地方。切削区的温度分布情况,须用人工热电偶研究金属切削加工过程中刀具与工件之间相互作用和各自的变化规律的一门学科。在设计机床和刀具、制订机器零件的切削工艺及其定额、合理地使用刀具和机床以及控制切削过程时,都要利用金属切削原理的研究成果,使机器零件的加工达到经济、优质和高效率的目的。
刀具磨损
刀具在切削时的磨损是切削热和机械摩擦所产生的物理作用和化学作用的综合结果。刀具磨损表现为在刀具后面上出现的磨损带、缺口和崩刃等,前面上常出现的月牙洼状的磨损,副后面上有时出现的氧化坑和沟纹状磨损等(图5)当这些磨损扩展到一定程度以后就引起刀具失效,不能继续使用。刀具逐渐磨损的因素,通常有磨料磨损、粘着磨损、扩散磨损、氧化磨损、热裂磨损和塑性变形等。在不同的切削条件下,尤其是在不同切削速度的条件下,刀具受上述一种或几种磨损机理的作用。例如,在较低切削速度下,刀具一般都因磨料磨损或粘着磨损而破损;在较高速度下,容易产生扩散磨损、氧化磨损和塑性变形。
刀具寿命
刀具由开始切削达到刀具寿命判据以前所经过的切削时间叫做刀具寿命(曾称刀具耐用度),刀具寿命判据一般采用刀具磨损量的某个预定值,也可以把某一现象的出现作为判据,如振动激化、加工表面粗糙度恶化,断屑不良和崩刃等。达到刀具寿命后,应将刀具重磨、转位或废弃。刀具在废弃前的各次刀具寿命之和称为刀具总寿命。泰勒提出的刀具寿命和切削速度之间相互制约的经验公式为
vTn=c
式中T为刀具寿命(分);v为切削速度(米/分);n和c为常数(与切削条件有关)。
生产中常根据加工条件按最低生产成本或最高生产率的原则,来确定刀具寿命和拟定工时定额。
切削加工性
指零件被切削加工成合格品的难易程度。它根据具体加工对象和要求,可用刀具寿命的长短、加工表面质量的好坏、金属切除率的高低、切削功率的大小和断屑的难易程度等作为判据。在生产和实验研究中,常以vT作为某种材料的切削加工性的指标,它的含义是:当刀具寿命为T分钟时,切削该材料所允许的切削速度。vT越高,表示加工性越好,T一般取60、30、20或10分钟。
加工表面质量
通常包括表面粗糙度、加工硬化、残余应力、表面裂纹和金相显微组织变化等。切削加工中影响加工表面质量的因素很多,例如刀具的刀尖圆弧半径、进给量和积屑瘤等是影响表面粗糙度的主要因素;刀具的刃口钝圆半径和磨损及切削条件是影响加工硬化和残余应力的主要因素。因此,生产中常通过改变刀具的几何形状和选择合理的切削条件来提高加工表面质量。
切削振动
切削过程中,刀具与工件之间经常会产生自由振动、强迫振动或自激振动(颤振)等类型的机械振动。自由振动是由机床零部件受到某些突然冲击所引起,它会逐渐衰减。强迫振动是由机床内部或外部持续的交变干扰力(如不平衡的机床运动件、断续切削等)所引起,它对切削产生的影响取决于干扰力的大小及其频率。自激振动是由于刀具与工件之间受到突然干扰力(如切削中遇到硬点)而引起初始振动,使刀具前角、后角和切削速度等发生变化,以及产生振型耦合等,并从稳态作用的能源中获得周期性作用的能源,促进并维持振动。通常,根据切削条件可能产生各种原生型自激振动,从而在加工表面上留下的振纹,又会产生更为常见的再生型自激振动。上述各种振动通常都会影响加刀表面质量,降低机床和刀具的寿命,降低生产率,并引起噪声,极为有害,必须设法消除或减轻。
切屑控制
指控制切屑的形状和长短。通过控制切屑的卷曲半径和排出方向,使切屑碰撞到工件或刀具上,而使切屑的卷曲半径被迫加大,促使切屑中的应力也逐渐增加,直至折断。切屑的卷曲半径可以通过改变切屑的厚度、在刀具前面上磨制卷屑槽或断屑台来控制,其排出方向则主要靠选择合理的主偏角和刃倾角来控制。现代人们已能用两位或三位数字编码的方式来表示各种切屑的形状,通常认为短弧形切屑是合理的断屑形状。
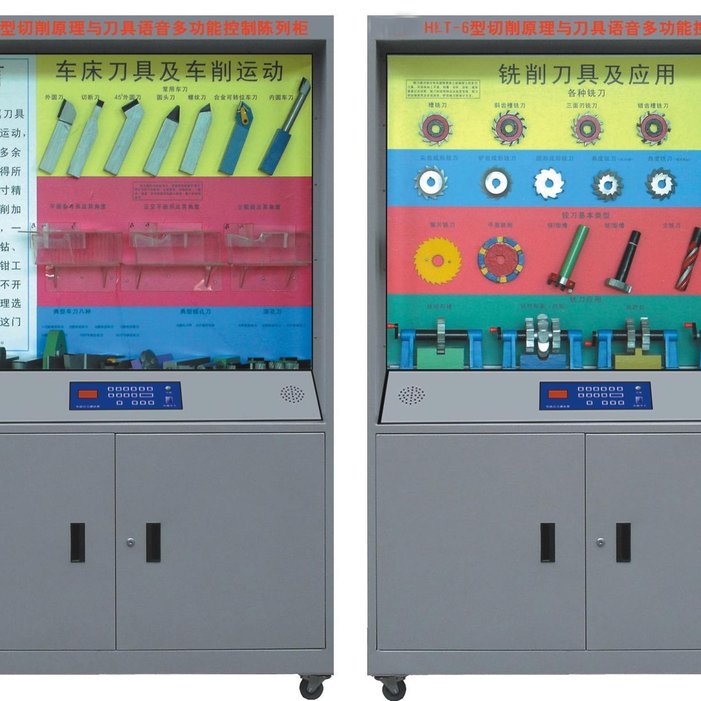
切削液 也称冷却润滑液,用于减少切削过程中的摩擦和降低切削温度,以提高刀具寿命、加工质量和生产效率。常用的切削液有切削油、乳化液和化学切削液3类。
相关应用
在设计和使用机床和刀具时,需要应用切削原理中有关切削力、切削温度和刀具切削性能方面的数据。例如,在确定机床主轴的最大扭矩和刚性等基本参数时,要应用切削力的数据;在发展高切削性能的新材料时,需掌握刀具磨损和破损的规律;在切削加工中分析热变形对加工精度的影响时,要研究切削温度及其分布;在自动生产线和数字控制机床上,为了使机床能正常地稳定工作,甚至实现无人化操作,更要应用有关切屑形成及其控制方面的研究成果,并在加工中实现刀具磨损的自动补偿和刀具破损的自动报警。为此,各国研制了品种繁多的在线检测刀具磨损和破损的传感器,其中大多数是利用切削力或扭矩、切削温度、刀具磨损作为传感信号。此外,为了充分利用机床,提高加工经济性和发展计算机辅助制造(CAM),常需要应用切削条件、刀具几何形状和刀具寿命等的优化数据。因此,金属切削原理这门学科在生产中的应用日益广泛,各国都通过切削试验或现场采集积累了大量的切削数据,并用数学模型来表述刀具寿命、切削力、功率和加工表面粗糙度等同切削条件之间的关系,然后存入计算机,建立金属切削数据库或编制成切削数据手册,供用户查用。
评论留言