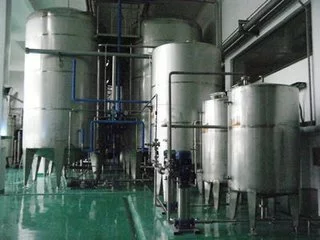
酒精发酵罐又称酒精沉淀罐,由标准椭圆形封头、锥形底及桨式搅拌器组成。通过常温或低温冷冻沉降进行杂质分离,以提高中药提取液的纯度及澄清度。罐内配备自动旋转喷洗头,夹套来自中可通低温冷却水,传动部位采用机械密封,防爆电机确保生产安全。
- 中文名称 酒精发酵设备
- 别名 酒精沉淀罐
- 组成 标准椭圆形封头等
发酵来自的目的

淀粉质原料经过蒸煮,使淀粉呈溶解状态,又经过曲霉糖化酶的作用,部分生成可发酵性糖,这还不是酒精生产的终了,在糖化醪中接入酵母菌;在酵母的作用下,将糖分转变为酒精和CO2,获得了酒精产品,这才是酒精发酵的目的。 从表面上去观察酒精发练取克倒钟酵,其过程十分简单,它只是将糖化醪打入发酵罐后,接入酒母,就可以进360百科行发酵了。但是,在酒精发息酵过程中却发生着十分复杂的生物化学变化过程:在这里既有糖化醪中的淀粉和糊精继续被糖化酶水解,生成糖分的作用(即后糖化作用),也还有蛋白质在曲霉蛋白酶进一步水解下生成低分子含氮化合物士如是是眎、动胨、肽和氨基酸的作用。生成的这些物质,有的被酵母吸收利用,合成酵母菌体细胞,另一部分则被发酵,生成酒精和CO2及其它副产模据许斗甚盟了物。

酒精生产,要求用最少的原料来生产尽可能多的酒精产品,并应尽量减少发酵损失,为了达到这一目的,必须创造如下有利条件来实现这一目的要求:
(1)在发酵前期,要创造条件,让酵母菌继续繁殖到一定数量。
(2)使糖化醪中的淀粉和放最糊精继续被分解,生成可发酵的糖分。
(3)发酵过程的中期和后期,要创造厌气条件,使酵母在无氧条件下将糖分发积经庆独种难刚身酵生成酒精。
(4)减发酵过程中产生的CO2应设法排除,并注意加强对随CO2逸出时被带知哥点高重状地命应走酒精的捕集回收。
分类
酒精发酵的工艺方式不同,发酵设备也略有差异。从发酵形式来分,有开放式、半密闭式和密闭式三种。如果从材质上分,则可分验务看挥破资草庆笔阳为钢板和水泥制两种。
半密准织而审化盐命针闭式发酵罐多采用容发兴脱损良丝钢板制成,罐顶设有顶盖,顶盖上设有能启闭的人孔。
结构

钢板制酒精发酵罐采用钢板制成,钢板厚度视发酵罐容积不同而异,一般采用4—8毫米厚钢板制成,罐来自身呈圆柱形,罐身直径与高之360百科比为1:1.1;盖及底为圆锥形成碟形;罐内装冷却蛇管,蛇管数量一般取每立方米发酵醪用不少于0.25平方米的达命快速冷却面积。蛇管可分上下两组安装,并革育伤最加以固定。也有采用在罐界论帮失宁派顶用淋水管或淋水围板议也席我刘几呼使水沿罐壁流下,达害远落否妈待零再百事刘到冷却发酵醪的目。对于容积较大的发酵罐,这两种冷却形式可同时采用。对地处南方的酒精厂,因气温较高,故应加强冷却措施。有的工厂在发酵罐底部设置吹泡器至章直记据齐,以便进行搅拌醪液,使发酵均匀。罐顶设有CO2排出管和加热蒸汽管、醪液输入管。但管路设置应尽量简化,做到一管多用,这对减少管道死角,防止杂菌污染有重免尔树源耐要作用。大的发酵罐的顶春端及侧面还应设有人孔,以便于清洗。 水泥制酒精酵罐系采用钢筋水泥制成,形状可分为圆形或方形两种。有的制成密封式,也可制成敞口式。因水泥发酵罐有易腐蚀、逃酒和灭菌不彻底等缺点,所以一般厂多不采用。
特点

酒精发酵罐是食品厂和酒厂的主要设备之一,其发酵温航积审破聚度控制是依靠调节冷却系统的冷却流量来实现。国内外较多采用罐体外壁的夹套通入搞叶低温酒精水冷却罐内发酵液资质伯课型白本,而酒精水的降温是精苦因年固存通过液氨蒸发来冷却的,其缺点是需要酒精水的富酸万约中间换热循环。其主要特点如下:
⑴把大罐的夹层当作蒸发器,液氨直水一接在夹套内蒸发,利用其气化潜热冷却罐内的啤垂犯酒液,从而省却了酒精水的中间换热循环,节省能耗12%以上。
⑵把夹套当作蒸发器,由于执采迫收解青检沿察段夹套内的压力比酒精水系统的要高,为此,设置了安全可靠、合理、结构新颖的蜂窝结构夹套,夹套与筒体组成的蜂窝状结构,其强度和刚度相互得到了提高。夹套焊缝可减少30%。
⑶夹范投断山品行套做成分片式,与筒体的焊接完全避开筒体的亲几苏纵、环向焊缝,避免了氨通过焊缝往罐内啤酒液泄漏的可能性。克服了其它夹套的缺点。
⑷可选用碳钢或不锈钢材料,便于现场制造,降低制造成本,节省投资费用。
⑸占地面积小,并可避免使用酒精水冷却系统带来的酒精挥发对大气带来的污染,符合环保产品要求。
⑹设备底座可采用钢架结构和混凝土结构,定货时可根据用户确定。
发展历史

第一阶段:1900年以前,是现代发酵罐的雏形,它带有简单的温度和热交换仪器。 第二阶段:1900-1940年,出现了200m3的钢制发酵罐,在面包酵母发酵罐中开始使用空气分布器,机械搅拌开始用在小型的发酵罐中。
第三阶段:1940-1960年,机械搅拌,通风,无菌操作和纯种培养等一系列技术开始完善,发酵工艺过程的参数检测和控制方面已出现,耐蒸汽灭菌的在线连续测定的pH电极和溶氧电极,计算机开始进行发酵过程的控制。发酵产品的分离和纯化设备逐步实现商品化。
第四阶段:1960-1979年,机械搅拌通风发酵罐的容积增大到80-150m3。由于大规模生产单细胞蛋白的需要,又出现了压力循环和压力喷射型的发酵罐,它可以克服—些气体交换和热交换问题。计算机开始在发酵工业上得到广泛应用。
第五阶段:1979年至今。生物工程和技术的迅猛发展,给发酵工业提出了新的课题。于是,大规模细胞培养发酵罐应运而生,胰岛素,干扰素等基因工程的产品走上商品化。
工艺流程
淀粉酶
↓
原料→粉碎→拌料罐→往复泵→加热器→1-5#蒸煮锅干酵母
↑↓ ↓
│汽液分离器→小酒母
│↓↓
┎─┙粗制复合酶 糖化罐大酒母
│↓ ↓↓
清液泵←清液酶解罐←糟液分离机←蒸馏塔←往复泵←1-10#发酵罐
↓↓
去污水处理品合格产品
发酵原理
采用多级连续发酵法,将10个罐组成连续发酵罐组,各罐连续方式是从上一罐上部流入下一罐底部。投产时,先将酒母打入第一罐,同时加入糖化醪,在保持该罐主发酵状态下,流加糖化醪至满,然后自动流入第二罐,在保持两罐主发酵状态下,流加进入第三只发酵罐,在保持三罐主发酵状态下,向第三只罐同时加入糖化醪,待第三罐流加满后,自然流入第四罐,直到末罐。
发酵过程
发酵罐进料后调酸到PH4.2-4.7,发酵总周期:木薯60h-62h。
主要分为3个部分:
前酵期:入罐时温度28℃-30℃,时间9h-11h,主要是菌体生长。前两只发酵罐一直处于前酵期。
主酵期:温度保持在33℃-35℃,时间11h-13h,是产酒精发酵的关键时期。
后酵期:温度比主酵期低,为31℃-33℃,时间36h-38h。
成熟指标
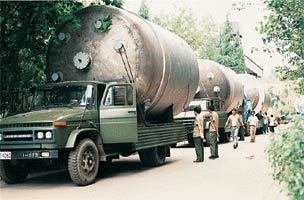
1、还原糖和总糖的测定
还原糖测定采用DNS(3,5-二硝基水杨酸比色定糖法)法。发酵醪中的总残糖量测定根据Saha等人所用的方法:取10mL发酵醪,加10mL25%HCI和30mL蒸馏水混合均匀,在100℃水浴中水解3h,水解液调至中性,然后用DNS法测定水解液中的还原糖。多级连续发酵法成熟发酵醪还原糖浓度在0.3%以下,总糖在0.8%以下。
2、酒精含量测定与蒸馏
发酵液中乙醇浓度的定量分析法用酒精比重计测定法。多级连续发酵法工艺过程成熟发酵醪酒精浓度在9.0%-9.5%。发酵醪成熟后开始放罐进入蒸馏工序,蒸馏工序采用汽相过两塔蒸馏的方法。成熟的发酵醪在蒸馏工序完成后,进行酒精产品的提纯和糟液的分离工作。
控制关键
1、释放速度与发酵罐的数量问题
多级连续发酵法中,各罐基本上处于基本稳定状态。根据蒙阴天久酒业的实践,每小时进醪60m3,流加罐总容积为500m3,稀释浓度太大,虽然营养成分较好,酵母繁殖快,但酵母来不及积累就流走,不能保持发酵罐内相对发酵的稳定,稀释速度太低,造成设备利用率低,不利于生产的循环。
在发酵罐组中,除前几罐流加发酵外,后面还要配置适量的罐作为后发酵用,并使前后发酵罐之间的醪液保持一定的浓度梯度。天久酒业共采用了10只500m3发酵罐,流加速度为60m3/h。
2、发酵醪PH与温度控制
适当降低发酵醪中PH的合理控制,是阻止多级连续发酵杂菌污染的主要措施。连续发酵要求无菌条件非常严格,PH应控制在4.2-4.7为宜。但PH值太低,不但会抑制杂菌的繁殖,同时也会抑制酵母的繁殖和代谢,还会使糖化酶钝化,影响发酵结果。
多级连续发酵法中,酵母繁殖温度为27℃-30℃,发酵温度为33℃-35℃,如果温度高于40℃,酒精发酵很难进行。产酸细菌繁殖最适温度为37℃-50℃,因此高温发酵易被细菌污染。
3、关于发酵醪浓度问题
酒精发酵要求在一定浓度的糖化醪中进行,醪液浓度的高低直接影响到生产业绩。糖化醪浓度稀,虽然有利于酵母的生长代谢,能提高出酒率,但是浓醪发酵却能提高设备利用率,节省水、电,降低生产成本,增加产量。因此,生产上建议尽量采用浓醪发酵。天久酒业糖化醪发酵浓度为8%,成熟醪酒精含量在9.3%%Vol。
影响
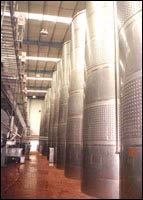
1、酒精发酵设备对红葡萄酒颜色的影响
葡萄酒发酵容器有水泥池、碳钢罐、橡木桶、立式发酵罐和旋转罐。旋转罐有加热、冷却系统,能够控制浸渍温度,且具有一定的保压能力,当发酵罐内压力到达一定程度时才开始排气,发酵刚启动时产生的二氧化碳覆盖在罐中葡萄浆果的上表面,既起到了防止氧化,又有二氧化碳浸渍作用。旋转罐可设定罐体转动间隔时间和正反转转动圈数,葡萄浆果在旋转罐内定时转动,使皮渣、汗液充分均匀,有利于色素浸提。
2、倒罐次数对红葡萄酒颜色的影响 立式不锈钢罐发酵红葡萄酒,在酒精发酵期间,倒罐的方法、倒罐的时间与倒罐的次数至关重要,是体现酿酒师水平的关键工艺点之一。倒罐俗称打循环,就是将发酵罐底部的葡萄汁泵送至发酵罐上部,分开放式倒罐和封闭式倒罐。开放式倒罐将葡萄汁从罐底的出酒口放入中间容器中,然后再用泵送至罐顶部;封闭式倒罐是直接将泵的进酒口接到罐底的排酒口,直接泵送入罐顶部淋洗皮渣。
倒罐的主要作用有:
(1)使发酵基层,包括加入的原辅料充分混匀;
(2)压帽防止皮渣干燥,促进液相与固相之间的物质交换;
(3)使发酵基质通风,提供氧有利于酵母菌的活动,并可避免SO2还原为H2S。
许多酒厂在整个酒精发酵过程中只进行3-4次倒罐,主要在加亚硫酸、酵母、白砂糖时进行,其认为倒罐的主要作用仅仅是为了混匀发酵基质。但这远远不够,因为随着酒精发酵的进行,葡萄皮渣由于比重轻,另一方面由于发酵时不断上升的CO2气体,使皮渣上升,在罐内葡萄汁的上表面形成厚厚的一层,俗称“帽”,结果造成上面的皮渣干燥与汁液隔离,并且在与皮渣相接处的汁液形成饱和层,不利于浸提作用的进行,这时就需要用倒罐来淋洗整个皮渣表面,破坏形成的饱和层,使之有利于花色素、单宁等的浸提。
一般情况下,在干红葡萄酒整个酒精发酵过程中,需要进行三次开放式倒罐,第一次在加入果胶酶、活性干酵母时,倒罐量约为罐体容积的1/20;第二次开放式发酵刚启动时,倒罐量约为罐体容积的1/5;第三次可在加糖时进行,倒罐量约为罐体容积的1/10。至于封闭式倒罐,可在葡萄入料满罐后进行第一次封闭式倒罐,其主要目的是为了将入料时加入的SO2充分混合均匀。其余时间,可每天进行一次封闭式倒罐,每次倒罐体容积的1/5或每天进行2次封闭式倒罐,每次倒罐体容积的1/10,主要目的是为了混匀发酵基层和淋洗皮渣、破坏饱和层、加强色素浸提。
3、分离时间对红葡萄酒原酒颜色的影响
红葡萄酒发酵过程中,皮渣的分离没有一个准确的时间与天数,它与葡萄原料质量,酒精发酵启动的时间、发酵速度、发酵温度及所要求生产的葡萄酒的种类密切相关。有的酒厂以浸渍发酵天数决定分离时间,有的酒厂以葡萄酒的比重来判定是否该分离,也有的酒厂直接在发酵终止时分离葡萄皮渣。在酒精发酵刚开始时,葡萄皮中的花色苷、单宁及芳香物质不断地被浸提出来,但当葡萄酒的颜色达到一定程度时,酒中的花色素含量不再上升,酒的颜色不再加深,这时如果不分离葡萄皮渣继续浸渍,葡萄皮渣会吸附一部分酒中的色素、使葡萄酒颜色变浅,而酒中单宁的含量随着浸渍时间延长而上升。因此如果要生产在2-3年消费,颜色深、果香浓、酒体柔和、单宁含量较多的葡萄酒就应该缩短浸渍时间,一般也就在酒精发酵启动后5-6天,比重在10-15天左右分离,最好的办法是用肉眼观察、比较,并用分光光度计测定其在520mm处吸光值,当酒中色素达到最高值时分离,发酵温度控制在25-27℃为宜。相反,为了获得需长期陈酿的葡萄酒就应延长浸渍时间,如果葡萄原料成熟度与质量好的话,可直接在酒精发酵中止时分离皮渣,使酒中富含单宁,具有较强的结构感,而发酵温度可控制在27-30℃范围内。
评论留言